Monday, 11 November 2024
How to Make a Pole Barn for a Custom Shop or Garage
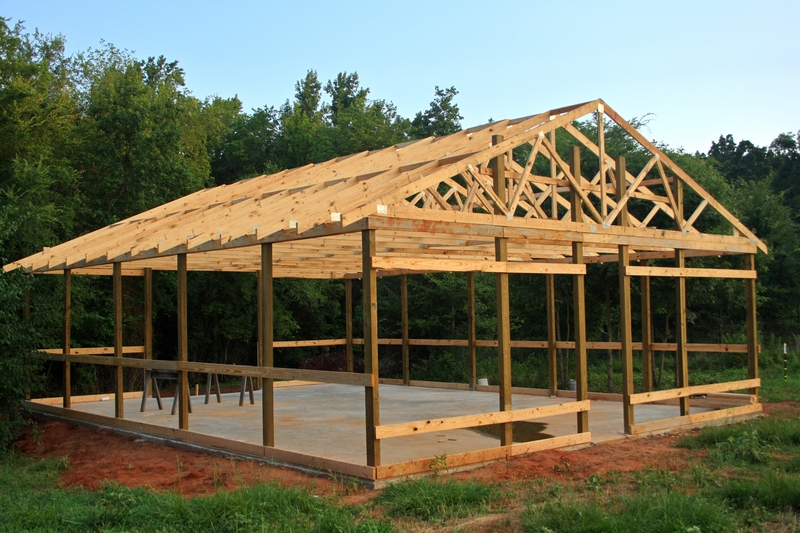
A pole barn, with its sturdy construction and adaptable design, provides an ideal solution for those seeking a spacious and functional workspace for their custom shop or garage. This guide will delve into the comprehensive process of building a pole barn, from initial planning to final finishing touches, ensuring a successful and rewarding project.
1. Planning and Design:
a) Defining Your Needs:
Purpose: Clearly define the intended use of your pole barn, whether it's for woodworking, automotive repairs, metal fabrication, or a combination of these. This will dictate the necessary space, layout, and amenities.
Size and Dimensions: Determine the required square footage based on your equipment, vehicles, and storage needs. Consider future expansion potential and leave room for maneuvering.
Layout: Sketch out a preliminary layout, including the placement of doors, windows, workbenches, storage areas, and any specialized equipment.
Climate Considerations: Factor in the local climate conditions. Ensure the barn's insulation, ventilation, and heating/cooling systems are sufficient to protect your tools and equipment.
b) Permits and Regulations:
Building Permits: Contact your local building department to inquire about required permits and zoning regulations. Obtain all necessary approvals before commencing construction.
Code Compliance: Familiarize yourself with local building codes regarding foundation types, roof slopes, wind resistance, and electrical requirements.
Setbacks: Understand and adhere to any setback regulations from property lines and public utilities.
c) Budget and Cost Estimation:
Material Costs: Research and compare prices for various materials, including poles, lumber, roofing, siding, insulation, windows, and doors.
Labor Costs: Determine whether you will handle the construction yourself or hire a contractor. Factor in labor costs and potential time constraints.
Contingency Fund: Allocate a percentage of your budget for unexpected costs and material price fluctuations.
2. Foundation and Pole Installation:
a) Foundation Preparation:
Site Preparation: Clear the building site of any vegetation, debris, and uneven terrain. Ensure proper drainage and consider installing a gravel base for stability.
Foundation Type: Choose a foundation type suitable for the soil conditions and anticipated loads. Options include concrete piers, concrete footings, or gravel pads.
Foundation Placement: Mark the location of each pole and excavate holes for foundation installation. Ensure the depth and dimensions meet local building codes.
b) Pole Installation:
Pole Selection: Choose durable and rot-resistant poles made of pressure-treated wood, steel, or concrete. Select the appropriate diameter and length based on the building's size and load-bearing requirements.
Pole Placement: Carefully position the poles within the excavated holes, ensuring they are plumb and level. Use concrete or grout to secure them in place.
Framing: Attach horizontal beams to the tops of the poles to create the structural frame of the building. Use strong bolts or lag screws for secure connections.
3. Wall and Roof Construction:
a) Wall Framing:
Wall Sheathing: Install sheathing over the pole frame to create a solid surface for siding and insulation. Use plywood, OSB (oriented strand board), or structural panels.
Insulation: Insulate the walls to enhance energy efficiency and create a more comfortable workspace. Choose an appropriate insulation type and thickness based on the climate and desired R-value.
Siding: Apply siding to the exterior walls, selecting from materials like metal, vinyl, wood, or fiber cement. Consider aesthetics, durability, and maintenance requirements.
b) Roof Construction:
Rafter Installation: Install rafters on top of the wall framing to support the roof structure. Choose the appropriate size and spacing based on the roof's slope and snow load.
Roof Sheathing: Attach sheathing to the rafters, creating a solid surface for the roofing material. Consider using plywood, OSB, or engineered panels.
Roofing Material: Select roofing materials suitable for your climate and aesthetic preferences. Common options include asphalt shingles, metal roofing, or tile.
4. Interior and Exterior Finishing:
a) Interior Finishing:
Drywall or Paneling: Install drywall or paneling to the interior walls and ceiling, providing a smooth finish and allowing for painting or wallpapering.
Electrical Wiring: Install electrical wiring, outlets, and lighting fixtures according to local building codes and your specific requirements.
Heating and Cooling: Install heating and cooling systems, considering the building's size, climate, and intended use.
Floor Covering: Choose a durable floor covering suitable for your workspace, such as concrete, epoxy flooring, or tiles.
b) Exterior Finishing:
Doors and Windows: Install doors and windows, considering their size, location, and functionality.
Gutter System: Install a gutter system to direct rainwater away from the building and prevent water damage.
Landscaping: Consider landscaping around the building to improve aesthetics and enhance drainage.
5. Final Touches and Customization:
Workbenches and Storage: Install workbenches, shelves, cabinets, and other storage solutions to organize your tools and equipment.
Lighting: Ensure adequate lighting throughout the workspace, considering natural light and supplemental artificial lighting.
Safety Features: Implement safety features such as fire extinguishers, smoke detectors, and first aid kits.
Personalization: Add personal touches to create a comfortable and functional work environment.
Conclusion:
Building a pole barn for your custom shop or garage offers a rewarding and cost-effective solution for a spacious and versatile workspace. By carefully planning, selecting materials, and adhering to building codes, you can create a structure that meets your specific needs and serves as a hub for your creative endeavors for years to come. Remember, this is just a comprehensive guide, and you should consult with local professionals and building codes for specific regulations and requirements in your area. With meticulous planning, careful execution, and a touch of personal flair, you can build a pole barn that becomes an extension of your passion and a testament to your craftsmanship.
No comments:
Post a Comment
Note: only a member of this blog may post a comment.